A Detailed Guide for Ancillary Packaging Materials
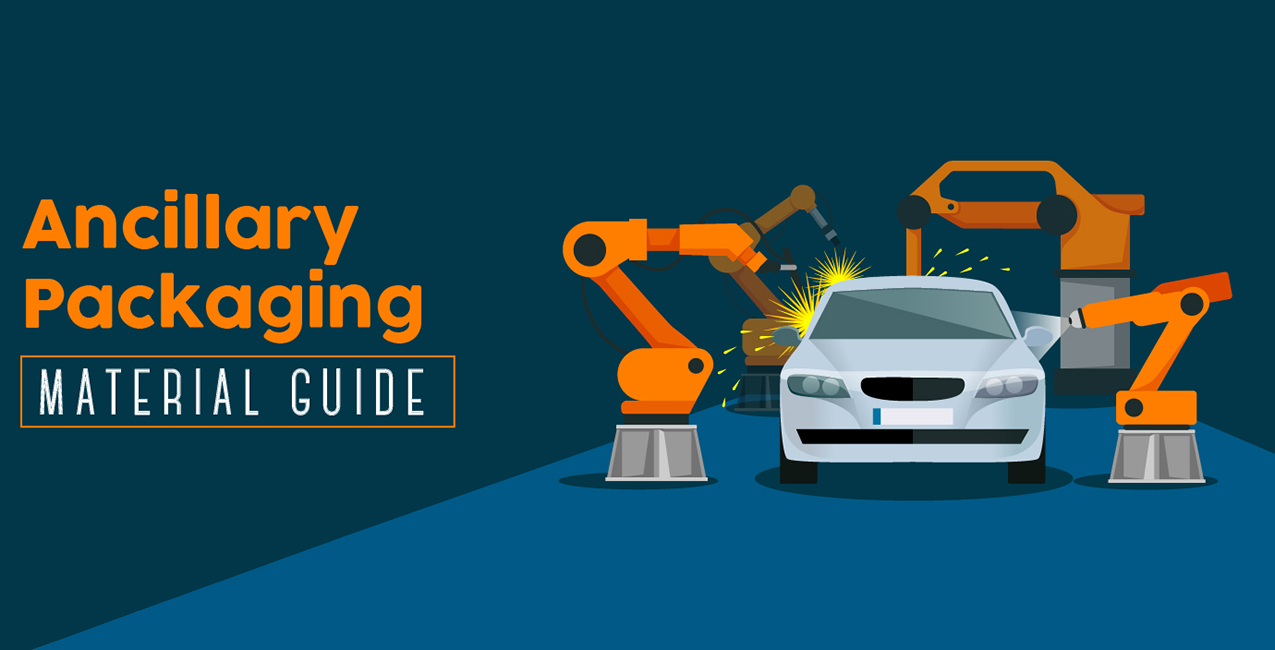
The ancillary packaging materials add value to the primary packaging in the automotive industry. It makes the automotive packaging functionally strong and sustainable for long-distance transit. Let’s discuss the types of auto-ancillary packaging materials and their importance for packaging in the automotive industry.
Caps and Closures
Caps and closures protect the automotive products like oil, grease, or chemicals over a stipulated time period. The functions of caps and closures are-
- Providing moisture barrier to prevent spoilage of products.
- Protecting volatile liquids.
- For the ease of opening, closing, and dispensing.
- Shielding the users from direct contact of automotive liquids. I.e. safeguarding users from the organoleptic properties of chemicals.
- Protecting the product from pilferage, tampering, or adulteration.
- Maintaining pressure and vacuum in the container.
The types of caps and closures available with automotive packaging suppliers are-
#1 Lids
Lids are removable or hinged caps for the containers. These are able to completely close the container and are suitable for smaller to large sized bottles. Lids are made of PP (Polypropylene), LDPE (Low-Density Polyethylene), HDPE (High-Density Polyethylene), Glass, or metal. Lids with a washer can provide vacuum sealing.
When to use lid caps?
You can use containers with lid caps for non-volatile liquids.
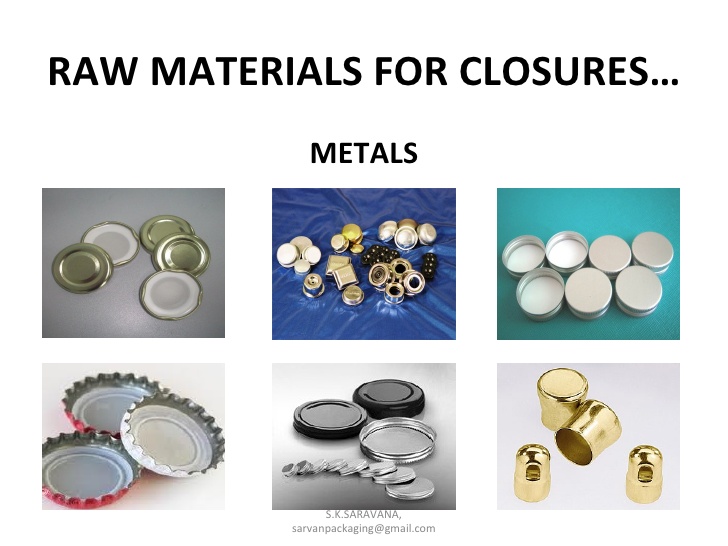
#2 Aerosol Valves
Aerosol valves are spray-dispensing systems. These are generally made of tin or HDPE plastics. Premium products also use aluminum aerosol valves and containers. The aerosol closures have 3 important parts- can, valve, and actuator.
When to use aerosol valves?
You can use containers with aerosol valve closure for painting and spraying oil when manual reach is not possible.
.jpeg)
#3 Threaded Closures
These are quick-opening closures for small and medium-sized containers. Threaded closures cover the container with a right-hand-screw locking system. They don’t vacuum seal but provide good protection both internally and externally. Many threaded closures come with a spout dispensing system. These are generally made of plastics and metals. Though, plastic threaded closures are more common because it's very cost-effective.
When to use threaded closures?
You can use containers with threaded closures for storing almost any type of liquids.
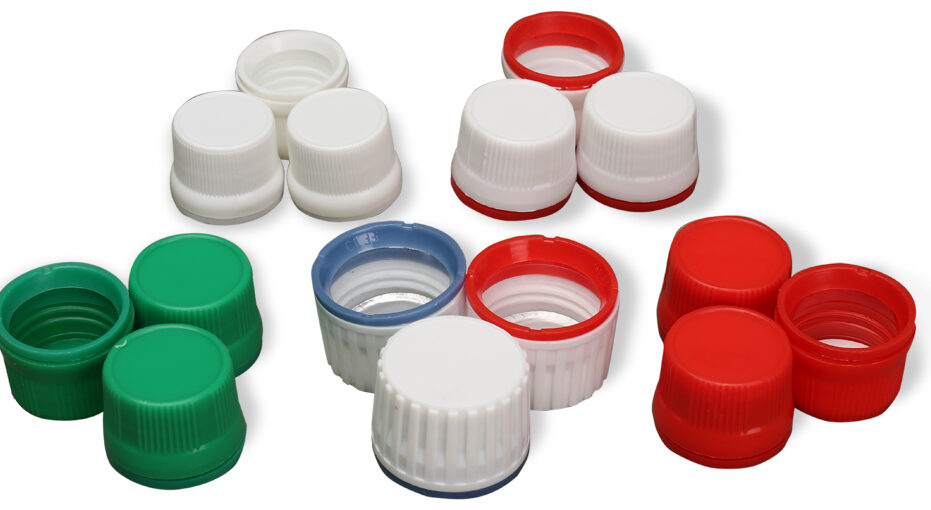
#4 Lug Caps
Lug caps are metal caps with a different threading system. Instead of continuous threads, they have lugs (barrier) and closes the container within a twist. Glass containers generally use lug caps.
When to use Lug caps?
You can use lug caps highly viscous liquids, pastes, and powders.
.jpeg)
#5 Crown Corks
Crown corks are a metal cap with crimps. Once open, these cannot reclose the containers. This type of closure is applicable to glass bottles.
When to use crown corks?
You can use containers with crown corks for single-use products.
.jpeg)
Things to Keep in Mind Before Selecting Caps and Closures for Auto-ancillary Packaging
- Dispensing mechanism
- Environmental stress cracking resistance
- Heat resistance
- Cost
- Thread matching tolerance
- Compatibility with the product, container, and container material
Inks
Inks are available in powder, paste, or solution form. They give a decorative effect to the substrate and are useful for labeling and printing. Inks can be pigments, dyes, or solvent additives. In the automotive industry, their application ranges over a variety of surfaces like paper, metal, cardboard, plastic, glass, textile, etc. Following are the types of inks-
#1 Printing
Printing inks have an application with the screen, offset, flexographic, and rotogravure printing processes. These are available as water-based and solvent-based products. Water-based printing inks are environmentally sustainable but expensive to use.
When to use printing inks?
You can use printing inks for labeling, branding, and describing mandatory product information.
.jpeg)
#2 Specialty
These are special types of ink useful for incorporating effects like night-glow, fluorescence, UV (ultraviolet rays) visibility, marking, and textile printing. For each effect, there is a designated specialty ink type.
When to use specialty inks?
You can use specialty inks for printing labels for internal automotive parts. Also, premium products manufacturers use this ink for sophisticated prints.
.jpeg)
#3 Surface Coating
The surface coating can serve both decorative and functional purposes. Varnish is the most common example of surface coating for protection against moisture. Rubber paint coating is also quite often used in the packaging industry. One can use colorful or transparent surface coating depending on requirements.
When to apply surface coating?
You can apply a surface coating to protect the packaging or automotive parts from the external environment.
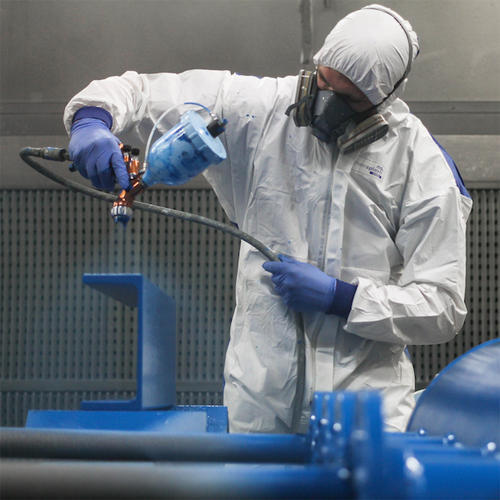
Things to Keep in Mind Before Selecting Inks for Auto-ancillary Packaging
- Type of printing process
- The surface of print application or substrate
- Drying process
- Type of finish you wish to have on the final product packaging
Adhesives
Adhesive or glue is a solid, liquid, or semi-liquid mixture, which binds similar and dissimilar materials. One can obtain adhesives from either natural or synthetic sources. Natural adhesives use starch, animal and plant protein, natural rubber, dextrin, and shellac. Whereas, neoprene and PVA (Polyvinyl alcohol) make synthetic adhesives. In between natural and synthetic adhesives, semi-synthetic adhesives are also available. Cellulose nitrate and polyamides are used for making semi-synthetic adhesives. Following are the types of adhesives.
#1 Water-based Adhesives
Packaging industry largely uses water-based (or water-borne) adhesives. These are safe to handle, energy and cost efficient. They also incorporate good binding strength.
When to use water-based adhesives?
You can use water-based adhesives in almost all types of automotive packaging.
.jpeg)
#2 Solvent-based Adhesives
Solvent-based (or solvent-borne) adhesives use volatile organic compounds as solvents or dispersants. They produce a very strong binding, but because of environment and safety regulations, there is a decline in their manufacturing. These are also more expensive than water-based adhesives.
When to use solvent-based adhesives?
You can use this adhesive for specific packaging, where water-based adhesives fail to incorporate appropriate binding.
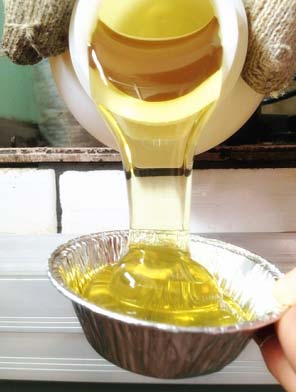
#3 Hot Melt Adhesives
These are solid adhesives made from thermoplastic polymers -generally, EVA (ethylene and vinyl acetate). Hot-melt adhesives are heated and applied in a molten state. Upon cooling, they form a bond between two surfaces. Glue guns provide ease of handling this type of adhesives.
When to use hot melt adhesives?
Because of their bond-formation speed, you can use them on a packaging line for high production rates.
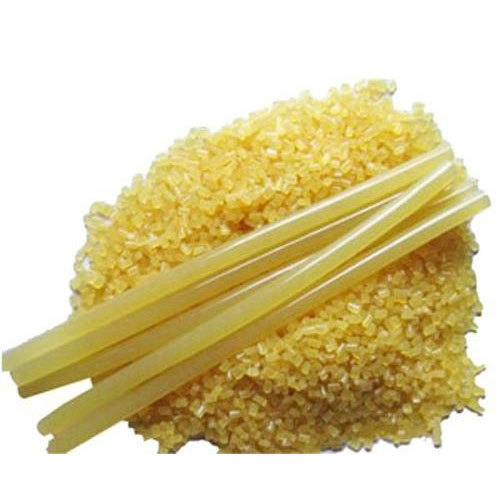
Things to Keep in Mind Before Selecting Adhesives for Auto-ancillary Packaging
- After application, the adhesive should be transparent
- It should not be hard and brittle
- It should not interact with the product and packaging
- Good adhesives have high thermal tolerance too.
Adhesive Tapes
Adhesive tapes are a combination of glue and a backing material. These are available in rolls. These are made of different materials like paper, woven and non-woven fabrics, foams, foils, films, to name a few. Following is the broader classification of adhesive tapes-
#1 Rubber-based Adhesive Tapes
Rubber-based adhesive tapes are cost-effective and easy to formulate. They offer high tack and adhesion.
When to use rubber-based adhesive tapes?
You can use rubber adhesive tapes for any packaging undergoing regular manufacturing and supply-chain processes.
#2 Acrylic-based Adhesive Tapes
This adhesive tape remains stable at above-normal temperatures. This makes it a good glue for packagings going through air-transit.
When to use acrylic-based adhesive tapes?
You can use this tape for temperature sensitive packaging.
#3 Silicon-based Adhesive Tapes
These are made from polymers of carbon and are very costly. But their adhesion is impeccable.
When to use silicon-based adhesive tapes?
You can use silicon-based adhesive tapes for packaging that requires withstanding temperatures above 155° C.
Things to Keep in Mind Before Selecting Adhesive Tapes for Auto-ancillary Packaging
- Temperature and pressure of production line and transit
- Cost
- Type of packaging
- Application.
Reinforcements for Auto-ancillary Packaging
Reinforcement enhances the strength of the packaging. They also help the packaging to withstand rough handling conditions. Following are the types of reinforcements.
#1 Metallic Reinforcements
These include steel straps and round wires. Metallic reinforcements are used with skids and pallets for unitizing loads.
When to use metallic reinforcements?
You can use metallic reinforcements for securing the packaging with a transport vehicle. Please note, metallic reinforcements are costlier than their plastic counterparts.
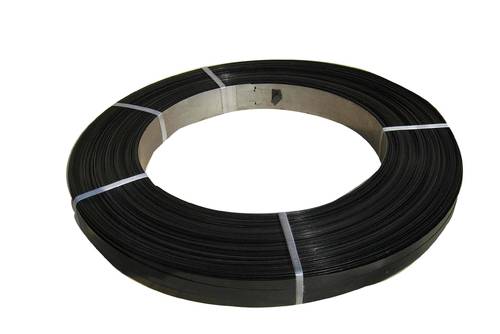
#2 Non-metallic Reinforcements
Non-metallic reinforcements include straps and rolls made from polyester, PET (polyethylene), PP (polypropylene), nylon, and rayon. PET straps are available in different standard colors. These are useful for color-coding the loads for easy identification in warehouses.
When to use them?
You can use non-metallic reinforcements (generally PET straps) for unitizing loads, material handling, and for securing the package against accidental loss or theft.
.jpeg)
Things to Keep in Mind Before Selecting Reinforcements for Auto-ancillary Packaging
- Tensile strength
- Surface retention (to provide non-slippery support)
- Welding strength
- Elongation recovery
- Reusability (especially in case of metal reinforcements)
- Use proper strapping equipment.
Clips
Clips are useful for retaining tension in auto-ancillary reinforcements (strapping). Following are the types of clips.
#1 Metal Clips
Metal clips are generally made of aluminum or stainless steel.
When to use metal clips?
If you are using metal straps, you should use metal clips for fastening.
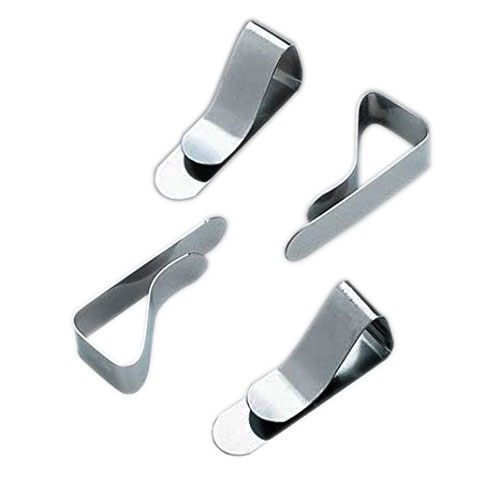
#2 Plastic Clips
Plastic clips are cheaper than metal clips. These are made of PET, HDPE, and LDPE material.
When to use plastic clips?
You can use them for fastening plastic straps.
Things to Keep in Mind Before Selecting Clips for Auto-ancillary Packaging
- Compatibility with the strap
- Quality of clip.
Cushions
Cushions protect the products in the package from shock or vibrations. They also prevent the packaging damage due to sharp edges of the products. If the packaging is not right-sized, cushions also act as void fillers. Following are the types of cushions you can use.
#1 Foam
Foams are a common cushioning material for auto-ancillary packaging. Polyethylene and polyurethane (or polyester) are the common materials for making foam. These provide extended protection against shock and prevent the package to break because of edgy products.
When to use foams?
If your product requires special resistance against wear, you can use foam-cushioning.
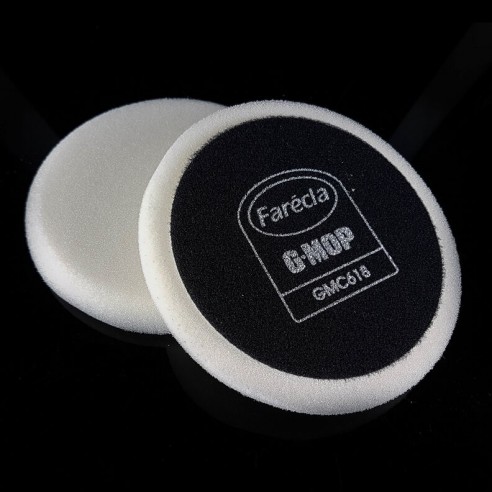
#2 Shredded Waste
Shredded cotton, paper, wood (Excelsior), textile, etc. provide good cushioning and fill up the packaging voids. If you are shipping greased or oiled machinery parts, these cushions are also capable of absorbing the extra oil and prevent leaking through the external packaging.
When to use them?
You can use shredded waste for automotive parts that don’t require special protection.
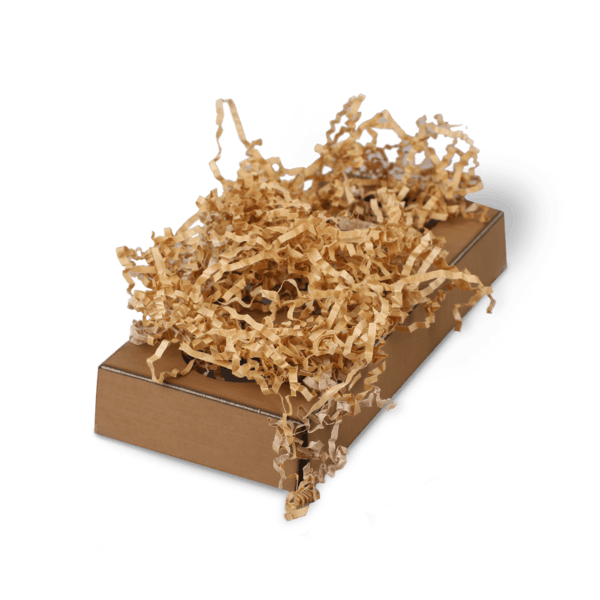
#3 Air Packets
Air packets are thin plastic tubes filled with air. Air packets take up more space and burst easily. Still, they are a good void filler. These are very inexpensive and can be used more than once until they break.
When to use air packets?
You can use them for non-sophisticated packaging.
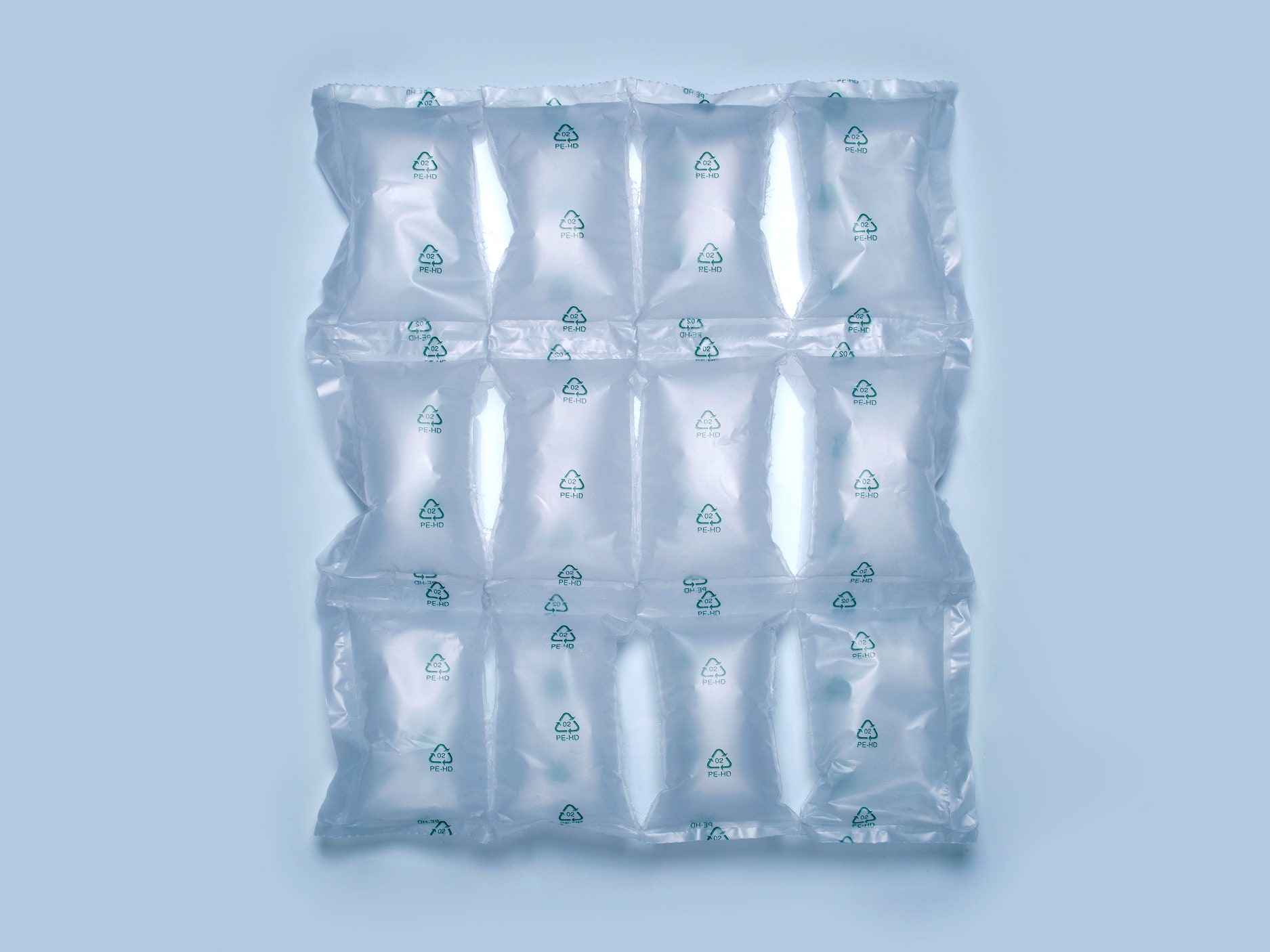
#4 Bubble Wraps
Bubble-wraps are plastic sheets with small air pockets. It is easy to wrap a product in a bubble wrap. You can wrap the product in multiple layers for added protection.
When to use bubble wraps?
You can use the same bubble wrap multiple times for packaging individual automobile parts.
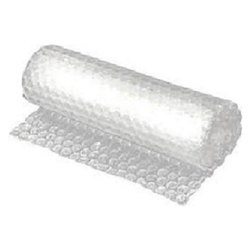
Things to Keep in Mind Before Selecting Cushions for Auto-ancillary Packaging
- Shock protection ability
- Cost and availability
- Sustainability with heavy machinery parts.
You can read in detail about different packaging fillers here.
Labels
Labels are important for indicating serial number, warnings, etc. on the automotive parts. They also serve as an area on the packaging for branding and mentioning other relevant information. The different materials used for making labels include metal, paper, BOPP (Biaxially Oriented Polypropylene), PP, PE, PVC (polyvinyl chloride), etc. In fact, some automotive parts label need to stay intact for decades. The type of labels common in auto-ancillary packaging is as follows.
#1 Adhesive Labels
These are sticky labels with the printed information on one side and adhesives on the other.
When to use adhesive labels?
You can use them for automotive oil packaging, external labeling, etc.
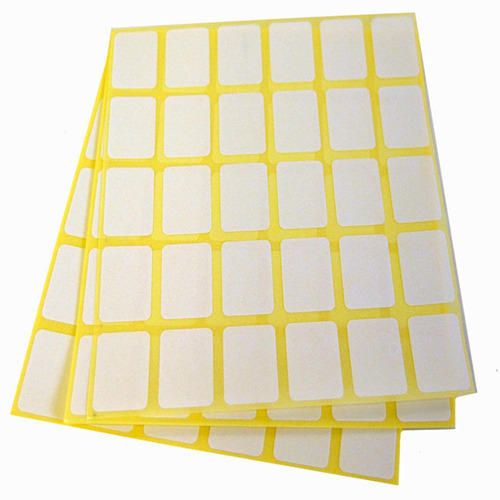
#2 Shrink/Stretch Sleeve Labels
Shrink and stretch sleeve labels cover the entire perimeter of the product and conform to the package’s geometry. These are generally made of LDPE. Stretch labels are highly elastic and can be pulled over the package. Shrink labels are applied loose and upon introduction to heat, they adhere to the package shape.
When to use them?
You can use shrink sleeve labels if your packaging is not prone to heat damage. Otherwise, stretch labels are better.
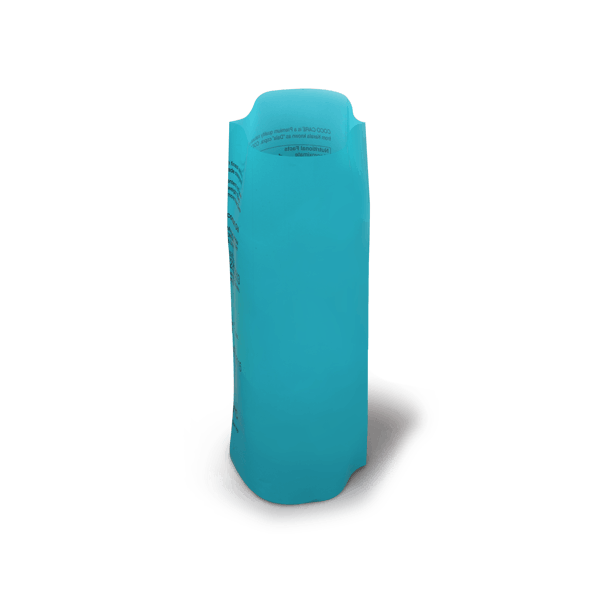
#3 In-mold Labels
In-mold labels are the inscribed plastic labels in the package through blow-molding, injection molding, or thermoforming process. This technique makes the label more durable, saves the labeling time but, increases the overall manufacturing time.
When to use in-mold labels?
You can use in-mold labels if you are bulk-manufacturing and want to save labeling cost.
Things to Keep in Mind Before Selecting Labels for Auto-ancillary Packaging
- Compatibility with the surface
- Environment to endure
- Material and printing cost
- Adhesive for sticking label on the package surface
Final Thoughts on Auto-ancillary Packaging Materials
Ancillary packaging definition states the packaging materials, which add benefits to the primary packaging. Auto-ancillary packaging materials prevent contamination, improve strength, bind packaging and safeguard the main packaging from damage during transit. Therefore, don’t overlook and use the right ancillary equipment for a durable automotive packaging.