9 Corrugated Box Testing Methods to Ensure Packaging Quality

As per FICCI, cardboard products make up more than 30% of the packaging industry. That’s because corrugated boxes are pretty popular. Regular slotted containers, for example, are one of the most widely used types of boxes for shipping and storage. Corrugated cartons are low cost, durable, and eco-friendly. However, not all boxes are made equal. That is to say, they vary a lot in terms of compressive strength, thickness, chemical resistance, and other factors.
You’ll need to know this when you have to choose a suitable corrugated box for your packaging needs. The cardboard strength and construction directly impact the amount of weight a box can carry. A box too weak might puncture or collapse. On the other hand, an excessive box means you pay extra for material and add to environmental wastage.
To determine how corrugated boxes hold up against external influences — so as to help you make an informed decision when picking boxes — manufacturers use multiple testing procedures.
Here’s a round-up of common corrugated box testing methods used to check the strength of corrugated boxes.
Corrugated Box Testing Methods:
- Bursting Strength Test
- Edge Crush Test 2 Single
- Water Resistance of the Gluing
- Cobb Sizing Tester
- Paper Grammage and Thickness
- Puncture Resistance
- Scuff Resistance Test
- Box Compression Test
- Chemical Analysis in Corrugated Box Testing
#1– Bursting Strength Test
- WHAT: Test box strength when subjected to pressure
- WHY: To determine exact weight a box can carry, rough handling
The Mullen Test or Bursting Strength Test checks the toughness of the walls of the corrugated board when subjected to force or pressure. In this testing procedure, a rubber diaphragm is used to apply pressure to the walls of the corrugated box until it bursts. The diaphragm is expanded using hydraulics and as the diaphragm expands, the corrugated board bursts under pressure.
We measure the bursting strength in Kilograms per square centimetre. The Bursting factor is given as a thousand times the bursting strength, divided by the grammage of the board.
Bursting factor = Bursting strength (kg/cm2) x 1000/Grammage (gm/m2)
#2 – Edge Crush Test
- WHAT: Cross-direction crushing of a corrugated board
- WHY: To test material quality, stacking strength, pallet shipping endurance
One of the most popular methods to test the stacking strength of corrugated boxes is the Edge Crush Test or ECT.

Every side of a corrugated box is made up of sheets that have three or more layers. Generally, a thin sheet with grooves and ridges is sandwiched between two flat sheets. These grooves and ridges, also known as flutes, provide anisotropic strength to a box. This means the boxes can bear a greater amount of force from one direction. Edge crush test, right test, or flat crush test helps determine this.
In the Edge Crush test, force is applied to one side of the box, perpendicular to the ridges, until the box gets crushed. In the Ring Crush test, a ring cut out from the box is used to test the same. While in the flat crush test, excessive force is applied on one side.
The results of the Edge Crush test are measured in pounds per lineal inch of load-bearing edge but represented as ECT.
ECT gives you an accurate idea of a box’s strength when they are stacked and shipped by pallets. Also, an ECT rated corrugated box uses less material than its equivalent Burst Test rated box, to provide an equivalent level of strength. This means it’s cheaper and less wasteful to purchase ECT rated boxes in bulk.
However, it is important to know that the above results (overall strength of a box) may vary based on the makeup of each corrugated sheet. Hence, knowing the type of corrugation is important before you make a decision.
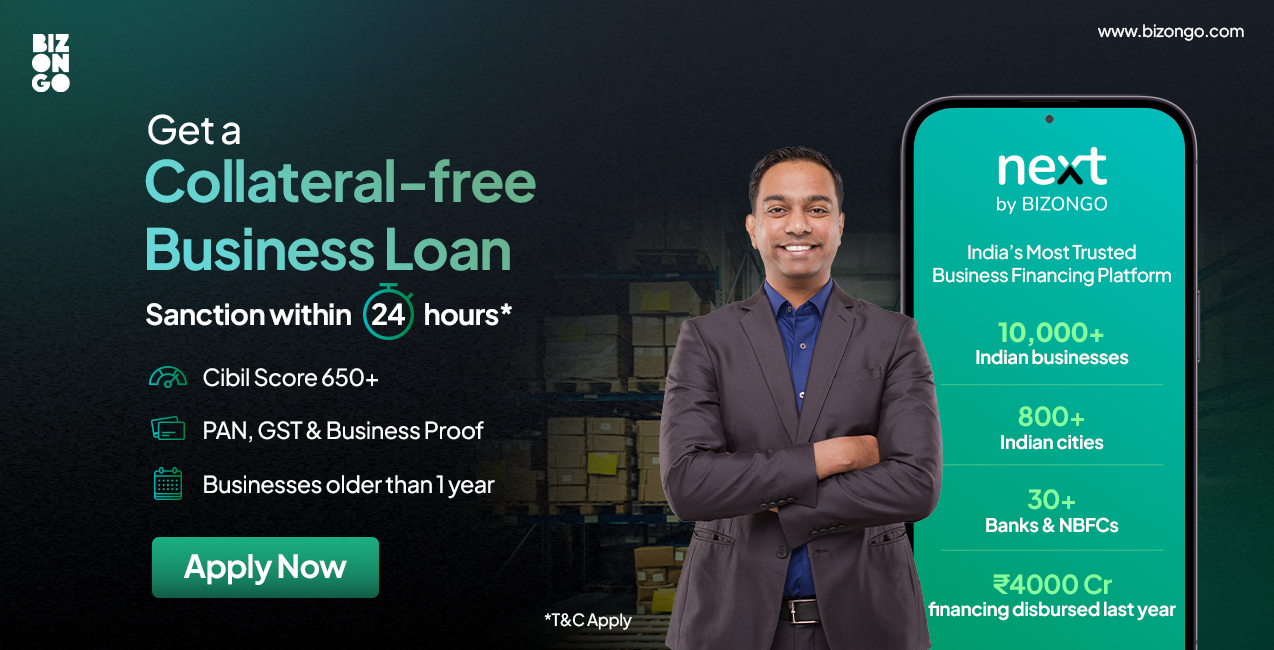
#3 – Water Resistance of the Gluing
- WHAT: Test water-resistance of the glue lines of a corrugated board
- WHY: To test the impact of climatic conditions, moisture permeability, water absorption
Even though the fiberboard itself can absorb and retain water, testing the water-resistance of gluing or sealing is also important. For certain applications, the FEFCO 9 standard is used to test the water-resistance of the gluing of the corrugated cardboard boxes.
In this type of test, the corrugated board is immersed in water while exposing the glue lines to check for bond strength and water absorption.
#4 – Cobb Sizing Tester
- WHAT: Check water resistance and measure weight increase when exposed to water
- WHY: To test the quality of the box, porosity
The raw material that is used in the manufacture of corrugated fiberboards has a tendency to absorb water and retain it. The Cobb Sizing tester is used to the degree to which water is absorbed.
In this test, corrugated fiberboard is first subjected to water. Then, the water is squeezed out of the sample using pressure. Usually, depending on the quality, all of the water is not removed in spite of the board being pressed by a heavy steel roller. The difference in weight because of the retained water is known as the Cobb value.
The lower the Cobb value the better the water resistance. The Cobb test is required for certain certifications, especially those involving hazardous material packaging.
#5 – Paper Grammage and Thickness
- WHAT: Test the areal density and thickness
- WHY: To test box quality and rigidity
Grammage and thickness are the two most fundamental properties of the corrugated fiberboards that determine the quality of the box. There is no “best” grammage or thickness mentioned in corrugated boxes specifications and it is completely based on your requirements.
When more padding is required, a box with a higher thickness is used. The flutes of the corrugated board are larger and pack more air in them. Thin boards with dense flutes have a high grammage. Such boxes are needed when the packaging should be more compact and rigid.

Thickness is usually measured in (millimetres) mm and grammage is expressed in terms of grams per square meter (g/m2).
Thinner boards are easier to fold, lighter, and more suitable when it comes to printing or detailing. Thicker ones are more sturdy and appropriate for heavy-duty shipping. Usually, the type of flute (A, B, C, E, or F) determines the cardboard strength with C being the most common (4.0mm).
#6 – Puncture Resistance
- WHAT: Test resistance to penetration by sharp, solid objects
- WHY: To test cardboard strength and sturdiness during transportation
Puncture resistance tests how well the box can handle the impact made with a pyramid or triangularly shaped weight. The corrugated box testing standards for puncture resistance include FEFCO 5 or ISO 3036.
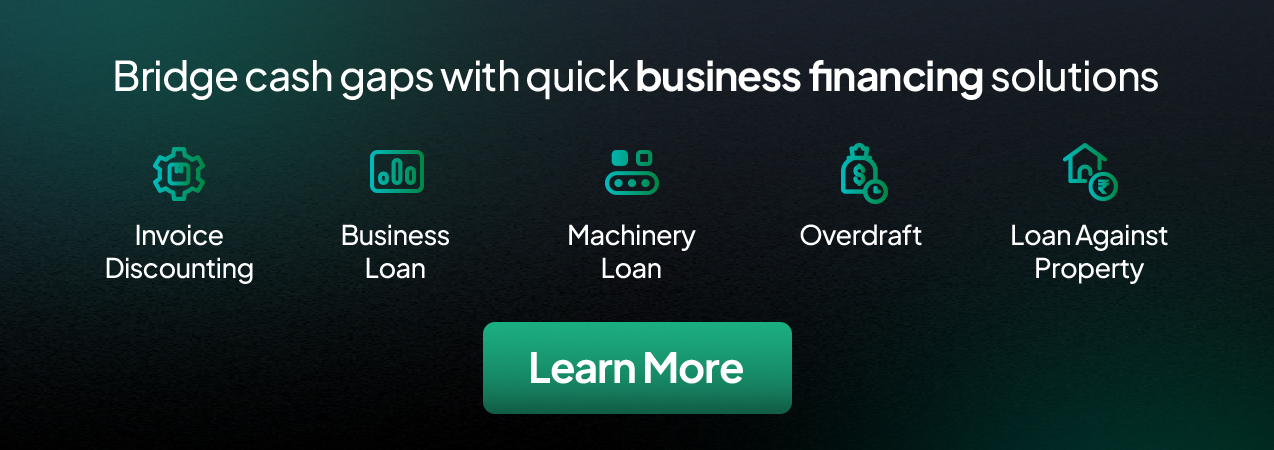
{{blog-form}}
#7 – Scuff Resistance Test
- WHAT: Check durability of printed or painted boxes to resist abrasion
- WHY: To ensure printed text on cardboard box can sustain rubbing, wearing
Printing is an integral part of packaging. With different types of printing methods being used, it’s important to check how well labels or prints can handle scuffing or abrasion. For this purpose, scuff resistance or rub proof tests are employed. There is the Sutherland Rub Test, which is an industry-standard testing procedure. Coated surfaces such as paper, films, paperboards and all other printed materials are tested using this procedure.
Alternative corrugated box testing methods are also available to test resistance to abrasion. These include rotary abrasion testers and even manual wiping. Scuff Resistance test is especially important for pharmaceutical or medical industries where label legibility is of prime importance.
#8 – Box Compression Test
- WHAT: Test compressive strength of a corrugated box
- WHY: To measure the stacking strength of a pallet load
Box compression test, also known as container compression test, is a way to test how much load the box can take on top of it before it gets deformed and the extent to which it gets deformed. It gives us a good idea of how many boxes can be stacked together without damaging the contents of the lowermost box. This test is crucial to check the strength of boxes and is required by most industries transporting boxes in bulk.

The boxes are tested in different orientations. If the box design makes use of inner supports, such as wood support or corrugated board cushioning, then such factors are also taken into account.
The compressive strength of a corrugated box can also be calculated using the McKee formula where the Edge Crush Test (ECT), Caliper or corrugated board thickness (CBT) and box perimeter (P) values are taken into account.
As per the McKee formula: Compression Strength = 5.874 * ECT * CBT0.508 * P0.492
#9 – Chemical Analysis in Corrugated Box Testing
- WHAT: Test resistance of box to chemicals
- WHY: To check product formulation and regulatory compliance
Chemical analysis is required for certain applications where the nature of fiberboard, as well as its resistance to certain chemicals, are checked. The analysis of the fiberboard involves microscopic examination of the board to see what types of paper are used to make the fiberboard. Moreover, the moisture content, as well as the pH of the board, is also determined.
Bizongo is India's 8th Largest Supplier of Corrugated Boxes! Watch how we can ensure 100% availability of corrugated boxes for your business.
Picking the Right Box for Your Needs
Corrugated box testing procedures help you determine the right kind of box for your business requirements. Most boxes carry a Box Maker’s Certificate stamp that lists specifications and box strength.
For example, the ECT value lets you calculate the amount of weight a package can carry. Or, the Box Compression Test helps determine stacking strength that’s especially important when shipping and transportation.
Take time to find the perfect box. It can save you a lot of costs and lower material wastage.
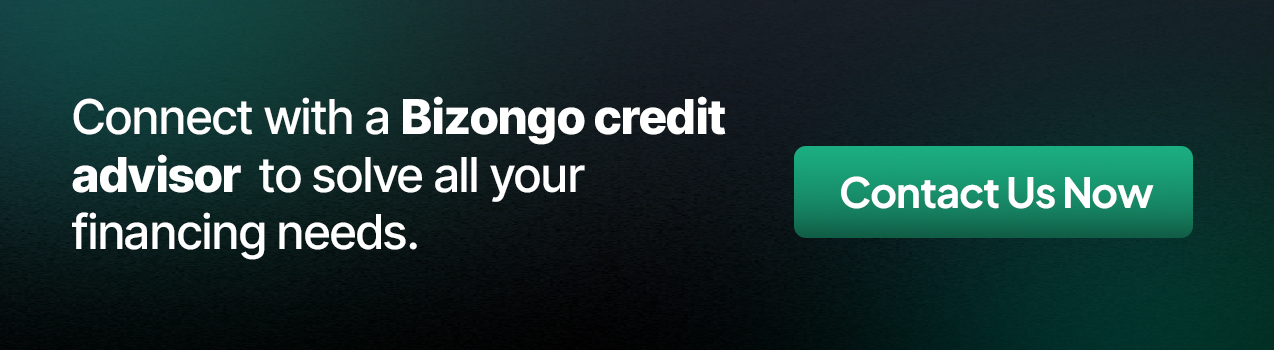