Flexible Packaging Testing Methods for Reliable Packaging
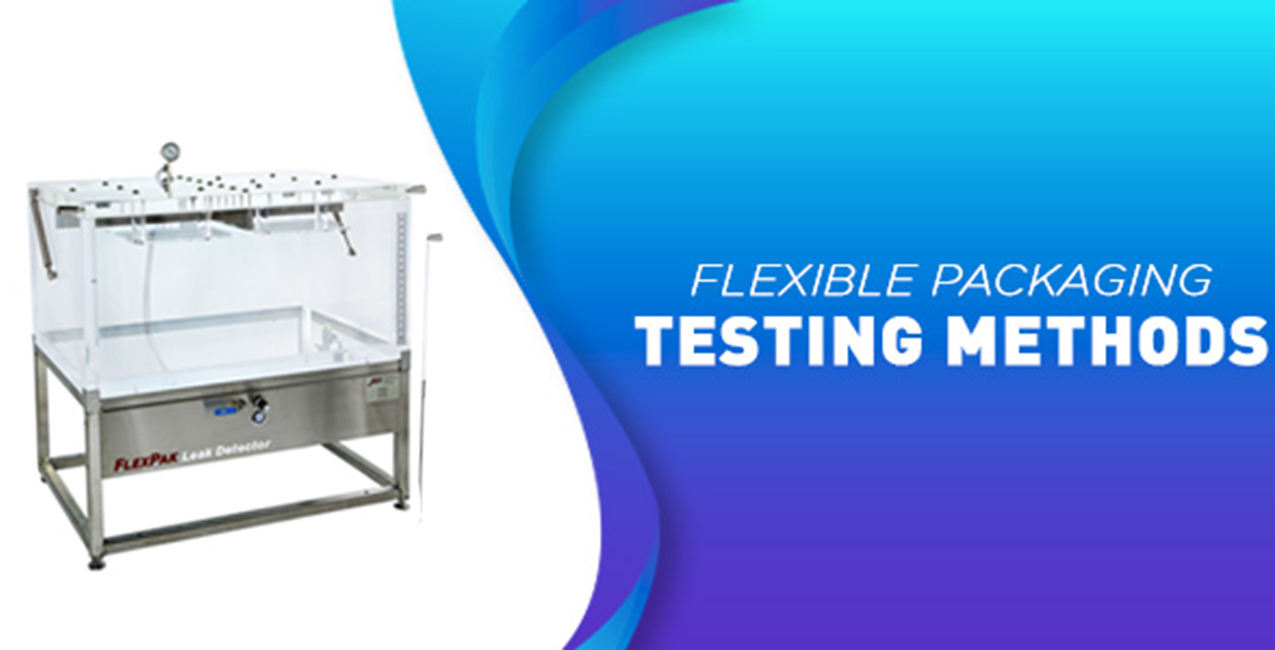
Testing a newly developed packaging is essential to ensure that the packaging serves its requirements in every situation. The external packaging often needs to sustain a lot of physical and mechanical stress. They also have to ensure that perishables remain fresh until the packaging is opened. To monitor how a packaging behaves under different kinds of stress, flexible packaging testing is quite important. Testing procedures for film and flexible packaging are quite different than testing for rigid packaging. For flexible packaging, a lot of extra parameters need to be tested too, such as barrier properties, flex crack resistance, seal strength and so on. There are government approved standard tests for testing flexible packaging. Here are some of the flexible packaging testing methodologies:
Flexible Packaging Testing for the Material of Construction
The flexible packaging materials testing checks the physical and chemical properties of the materials that are used to make flexible packaging. For example, flexible packaging films like ordinary cling film or shrink film goes through the tests that include tensile strength, elongation, surface energy, elastic modulus, moisture vapor, and oxygen transmission rate, heat sealing strength, heat sealing conditions and so on. The chemical properties testing generally involve checking its reactivity with the food items or products that it will contain under different conditions.
#1. Dimension Testing
The flexible packaging testing for dimensions checks the size of the packaging before and after it is filled. Flexible packaging changes its shape based on the contents inside. Therefore, it is quite essential to check the packaging both when it is empty and when it is filled. The standard tests include testing the length, breadth, and depth. Dimension testing also involves testing the grammage of the film used to manufacture the packaging. We commonly measure grammage as grams per square meter or GSM. Higher GSM numbers imply a denser and heavier film. GSM inversely correlates with the yield. The yield of a film determines much surface area unit weight of the packaging will cover. It’s measured in square meters per kilogram – just the opposite of GSM. Dimension testing is essential since, in a lot of cases, manufacturers use assembly lines to fill the packaging. To ensure that the packaging can integrate seamlessly with the assembly line, dimension testing is done.
#2. Testing for Mechanical properties
This suite of tests involves checking how much physical and mechanical stress the packaging can take before it breaks. This includes the following tests.
A. Tensile Strength
This test checks how much force is required to break the flexible packaging and how much it can be elongated before it breaks. This also gives the elongation to failure data – that is how much a material can be stretched.
B. Dart Impact
The dart impact test, often known as the drop dart test, checks the toughness of the flexible packaging. As the name implies, a dart is released from a certain height which free-falls onto the flexible packaging, which is clamped tightly at the base. Darts of different weights are used in the test.
C. Bond Strength (PET, Poly)
Bond strength determines how strong the lamination is. Flexible packaging often contains multiple layers of polymers, including metalized sheets. The bond strength test checks how much force is needed to take the layers apart.
D. Seam Strength
Seam strength checks the strength of the packaging in the areas where two films or sheets are joined.
E. Flex Crack Resistance (FCR)
Flex Crack Resistance tests how brittle flexible packaging is. This flexible packaging testing method checks how much the packaging can be flexed or bend before it cracks.
F. The Coefficient of Friction (CoF)
CoF checks how easily two surfaces slide against each other. In other words, it tests the smoothness of the film or the packaging. CoF gives an idea of how easily packaging films can slide over another material during packaging.
#3. Testing of functional properties
The functional properties test the barrier properties, understand the dissolution, diffusion, adsorption of the flexible packaging materials. They also help understand how capable the packaging is when it comes to preserving the products.
#1. Water Vapor Transmission Rate (WVTR)
This test checks the permeation of the material by water vapors at a selected temperature, pressure and humidity. The transmission rate is measured as grams per square meter per day, that is, how much water vapor is transmitted through the packaging film per unit area per unit time.
#2. Oxygen Transmission Rate (OTR)
This test uses the packaging film to form a barrier between a chamber devoid of oxygen and filled with oxygen. Like the WVTR test, it is measured in moles per square meter per day.
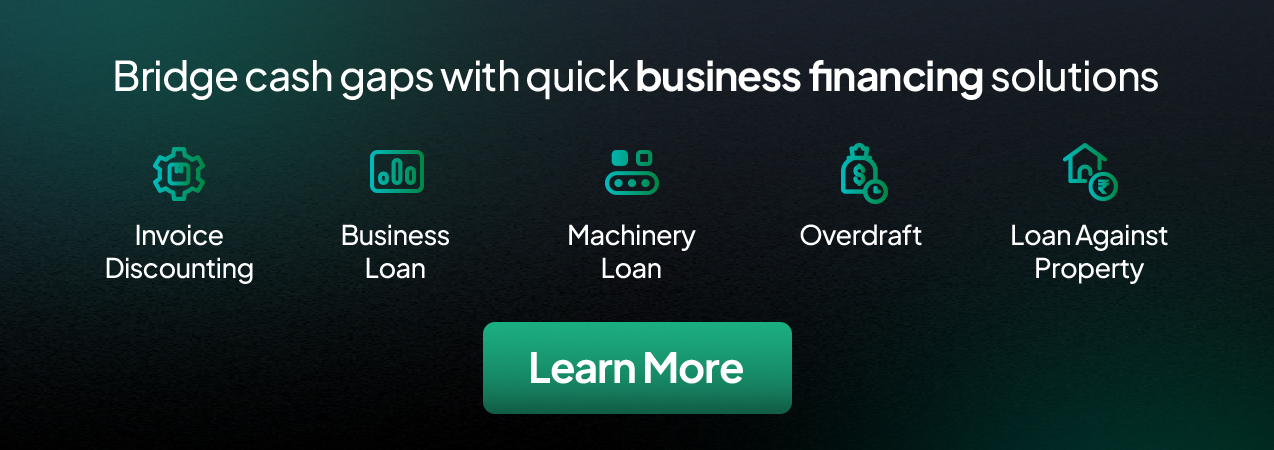
{{blog-form}}
#4. Packaging Strength and Integrity Tests
This set of tests check how well the packaging is sealed in the assembly line and how well it holds over time. Even if the materials used for packaging have excellent barrier properties, an improper seal can make the product expire earlier than expected. Most of these tests occur while the package is filled with the product.
package testing - flexible packaging testing
#1. Seal Strength
This flexible packaging test shows how secured the seal is and how well it keeps the packaging enclosed over time.
#2. Drop Test
Drop test checks whether the flexible packaging can survive drops when it is filled. To pass a drop test, neither the materials used to make the packaging nor the seal should break. Also, the product inside should stay intact.
#3. Vibration Test
This checks how well the package can endure vibrations.
#4. Compatibility Test
Compatibility tests are quite important to understand that the product shelf-life in the packaging. This flexible packaging testing checks if the product inside is compatible with the materials used to make the packaging and the sealing method. Incompatible packages can often lead to leakage or product spoilage.
#5. Scuff Proofness
This checks the durability of the packaging against scratches.
#6. Leakage Test
Leakage tests check if the seams, seals or the materials of the packaging leaks or not by putting the packaging filled with the product in a vacuum chamber. The pressure is dropped gradually and the package is checked continuously for any signs of leakage.
flexible packaging leak test setup
#7. Global Migration
Migration testing assesses the toxicological risks associated with the packaging. Many chemical substances used in food packaging are often toxic but are used for their barrier properties, or for increasing the strength of the packaging film. Global migration checks how all the materials used in the packaging can contaminate the food. In other words, it checks how inert the materials are.
#8. Environmental Stress Crack Resistance (ESCR)
ESCR checks how resistant the packaging is to Environmental stress cracking or ESC. ESC is quite common in plastics since they become brittle over time through exposure to UV and reaction with other reagents.
#5. Visibility and Appearance Test
Optical properties of flexible packaging are also quite important. They make up a major part of the branding. They also improve product visibility. The color, haze, and gloss are tested.
#1. Color Fastness
Color fastness is tested by exposing the packaging to agents that can cause the color to fade.
#2. Haze and Gloss
Haze is tested using a Spectrophotometer whereas gloss is tested using a Glossmeter.
Bottom-line
Testing is crucial for any type of packaging and makes up an important part of quality control. This allows manufacturers to understand how long their product will last on the shelf, or if they will survive the shipping. Flexible packaging testing is an investment that can save a lot of money in the long run.
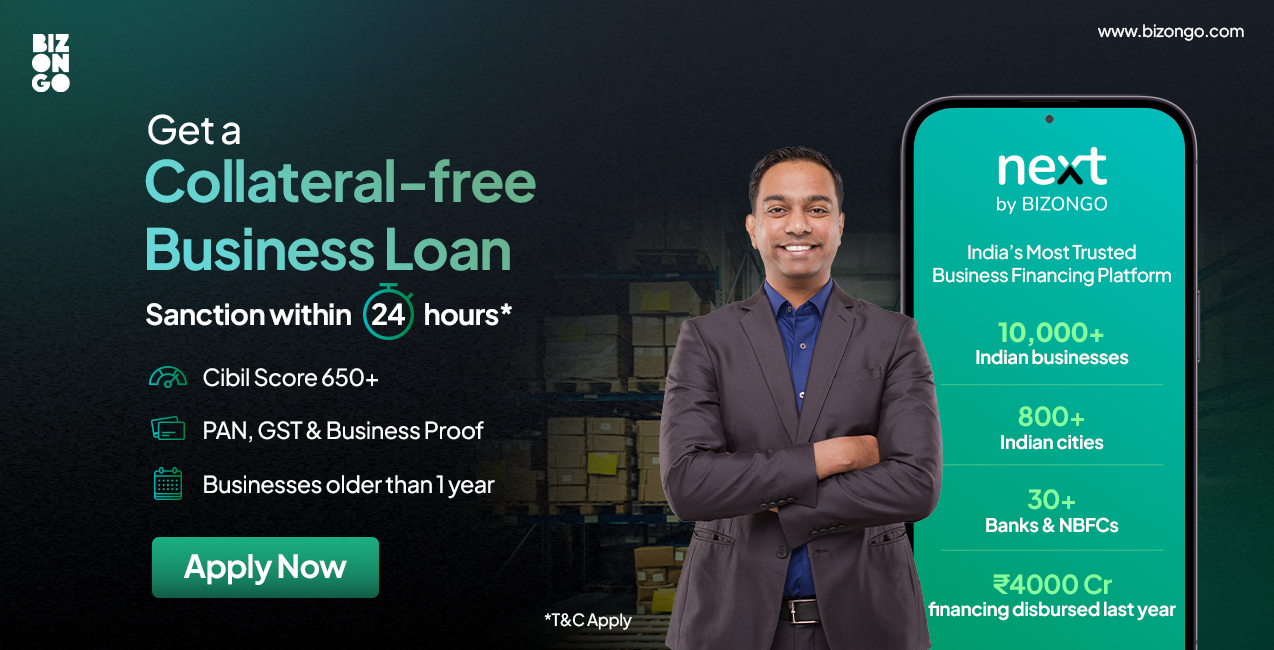
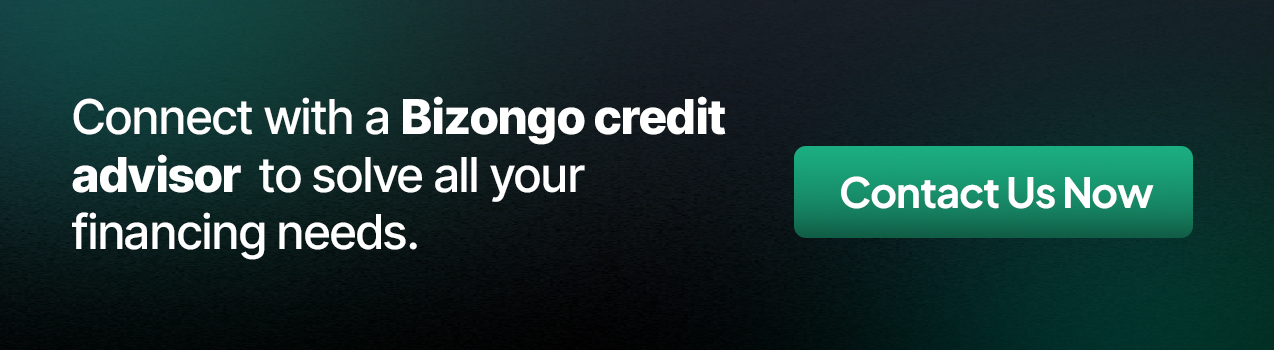