Picking the Right Packaging Printing Method for Cartons
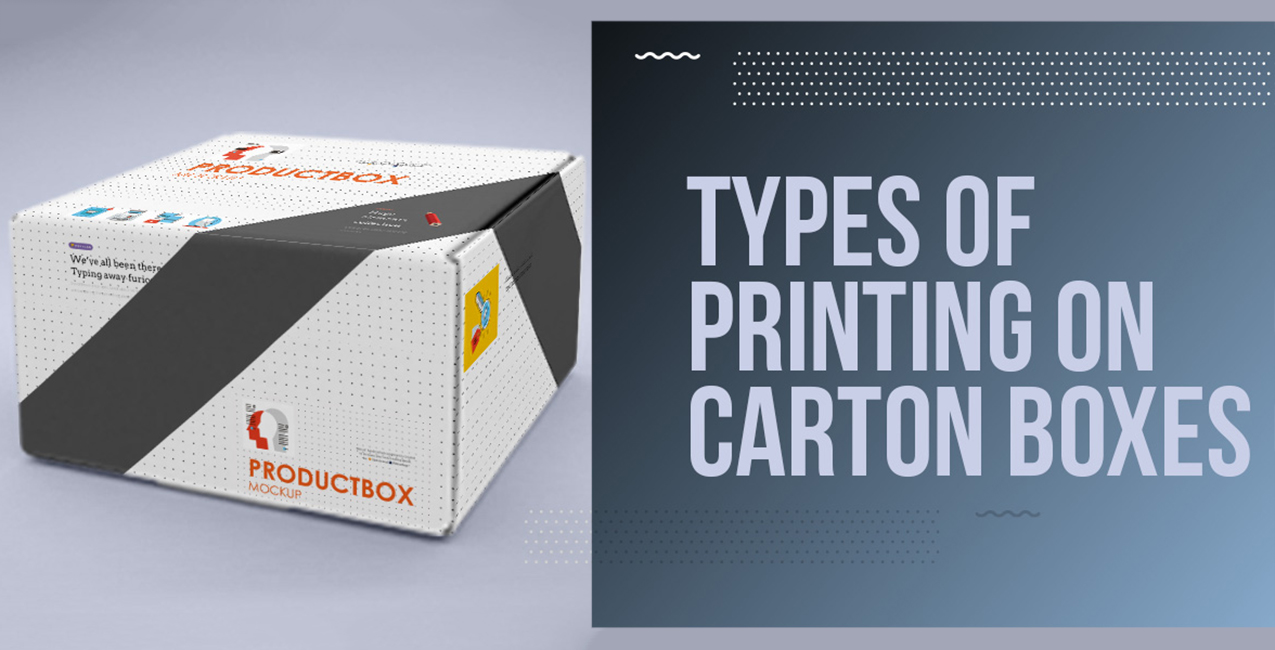
Packaging printing can be an extensive subject and picking the right type of printing can be quite confusing if you are not aware of the processes as well as the pros and cons. When you ask for a quote to your packaging manufacturer, you are only limited to the printing technology that they have access to. However, your decision should not be limited by that. Since cartons are rigid and flat, you can get a lot of printing options that other flexible packaging materials do not have. Here are some of the common printing technologies that are available for printing cartons.
Lithography or Offset Printing
Lithography is used for most modern-day bulk printing jobs. Manufacturers use printing plates for lithography. The plates are inked and then pressed onto the paper for printing. Modern-day lithography uses rollers instead of printing plates. The rollers contain the negative of the image that is made by exposing an emulsion t ultraviolet light. Lithography is mostly used to print folding cartons as well as labels, which are also referred to as litho labels.
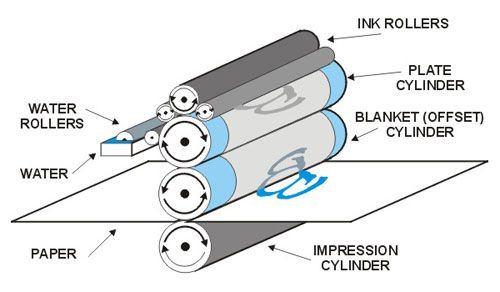
Lithography provides you with retail-quality printing. Cosmetic boxes, electronic products, and food packaging printing make use of lithographic technology. Lithography has very high print quality. More than four colors can be used in lithography. However, 1 or 2 colors are used commonly. Lithography also allows special coatings to be applied. This gives the product packaging an up-market look. It can be used to give a soft matte touch or a high gloss look. Lithography also produces smooth color gradients where banding is not noticeable.
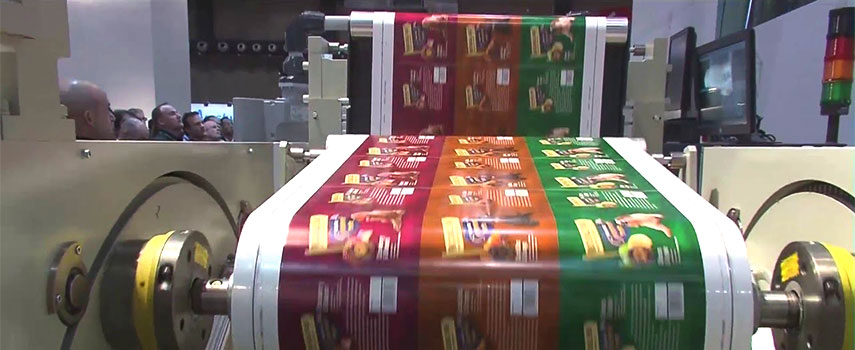
The biggest drawback with lithography is the tooling cost and the lead time. To make sure that the costs stay low, one has to order high volumes of printing. Many lithographers have a high minimum number of prints that you have to order. Also, lithography printing can only be done on flat surfaces.
Flexography Printing
Flexography is commonly used for stand-up pouches. However, manufacturers use it for corrugated boxes too. The method is quite similar to that of Lithography, but instead of flat plates, a flexography uses a light-sensitive polymer. A 3D relief is prepared which is then mounted on a roller to print the graphic. In Flexographic printing, your cost of printing will go down. Plus, tooling costs are much lower. Only the plate needs to be prepared. It has faster turnaround time and can use both water and oil-based inks.
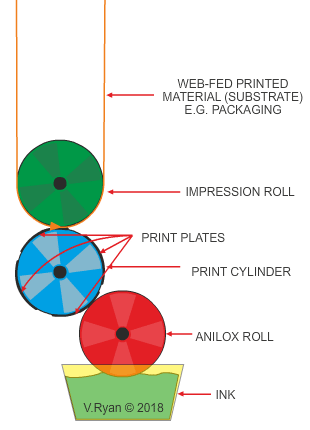
Compared to lithography printing, flexography has noticeably lower printing quality. It cannot be used for printing photo quality images. Moreover, while printing smooth colors or gradients, flexographic printing has visible banding. Registration with 4 color processes is also much more difficult.
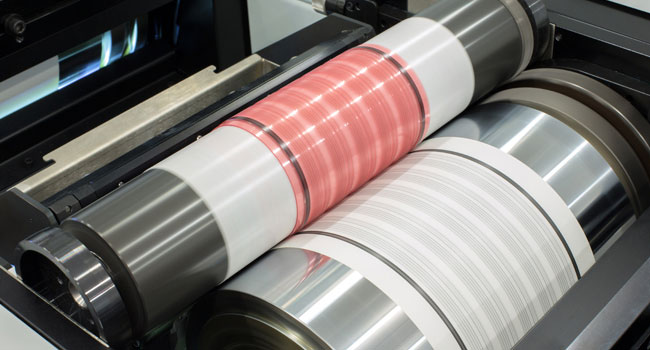
Read: Flexographic v/s Lithographic Printing
Digital or Inkjet Printing
Digital printing is extensively used in small-scale print jobs. When it comes to paper products, digital printing is used quite a lot. Labels, films for flexible packaging, folding paper cartons, corrugated boxes – all of them use digital printing. Even packaging prototypes make use of digital printing.
Digital printing is quite easily accessible. This is because it comes with zero tooling costs. No prior setup is required. You can just go to the manufacturer with a design and get it printed right there. Most printing companies also have a low minimum order quantity when it comes to digital prints. It has quick turnaround times and with the correct configuration, it gives printing quality that is comparable to lithographic printing.
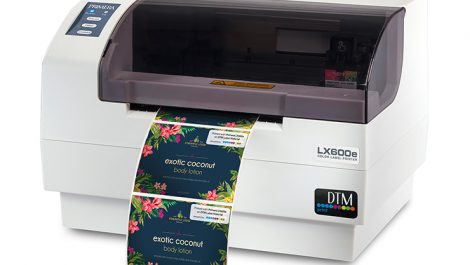
Digital packaging printing is inconvenient to print in large volumes. This is mostly because it takes a lot of time to print a single sheet. Moreover, digital printing requires color calibration. Digital printing does not come with any protection, like lithographic printing. Moreover, digital costs cannot use metallic inks and per unit costs are quite high, compared to lithographic or flexographic printing.
Rotogravure
Rotogravure is typically used for stand-up pouches. Folding cartons also use this technique. Rotogravure process consists of an engraved cylinder that is used to transfer the ink to the substrate. The engraved cylinder presses the paper or film onto the gravure cylinder which is smeared with the ink. Rotogravure is not very common when compared to flexographic or lithographic printing, but is still used in commercial printing. It can provide premium quality prints with calibrated colors, has 4 color process and can easily add PMS colors. Rotogravure printing also provides very long lasting prints.
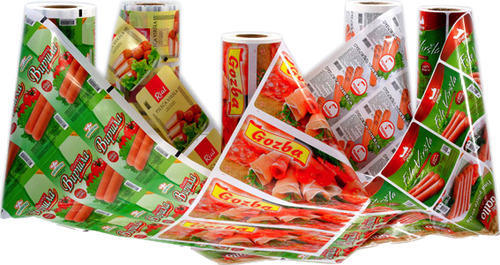
Tooling costs are quite high in this process of printing. Therefore, if you are investing in this process, you better order a high print volume. The complicated tooling also increases the lead times.
Silkscreen or Screen Printing
Silkscreen is used for printing labels, folding cartons, promotional items and also for prototypes. It is a great option for custom packaging printing especially when the packaging is made independently. This includes caps and bottles, custom-made mugs and shirts. The set-up cost is also quite minimal. A polymer mesh is used to transfer the ink to the substrate. Here, the mesh acts as a stencil. A squeegee is used transfer the ink through the mesh and onto the surface. Silkscreen can also be used for smaller volumes and does not always need a flat surface.
The production speed with silkscreen is much lower. A lot of the process requires manual effort and hence human error may screen in. Moreover, the print quality is quite low, colors are not accurate and is not a good option for high volume printing.
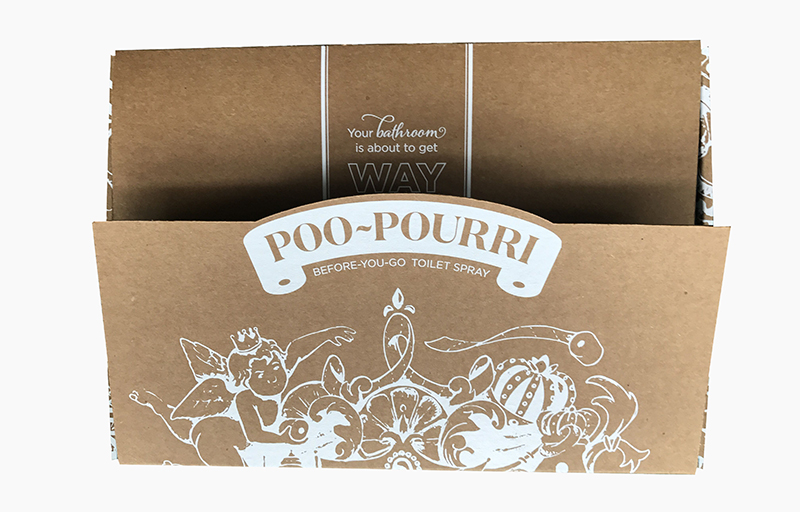
What’s Right for You?
The best printing solution depends on your requirements and your budget. If you want high-quality prints with accurate colors, flexography should be your first preference, followed by lithography. For smaller volumes, you can also go for digital printing. If color accuracy is of utmost importance to you, then you can go for Rotogravure printing too. A silk screen is a good option for low cost and low volume projects.
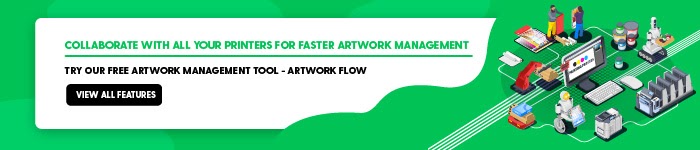