Struggling With Packaging Stock-Outs? Here's What You Can Do
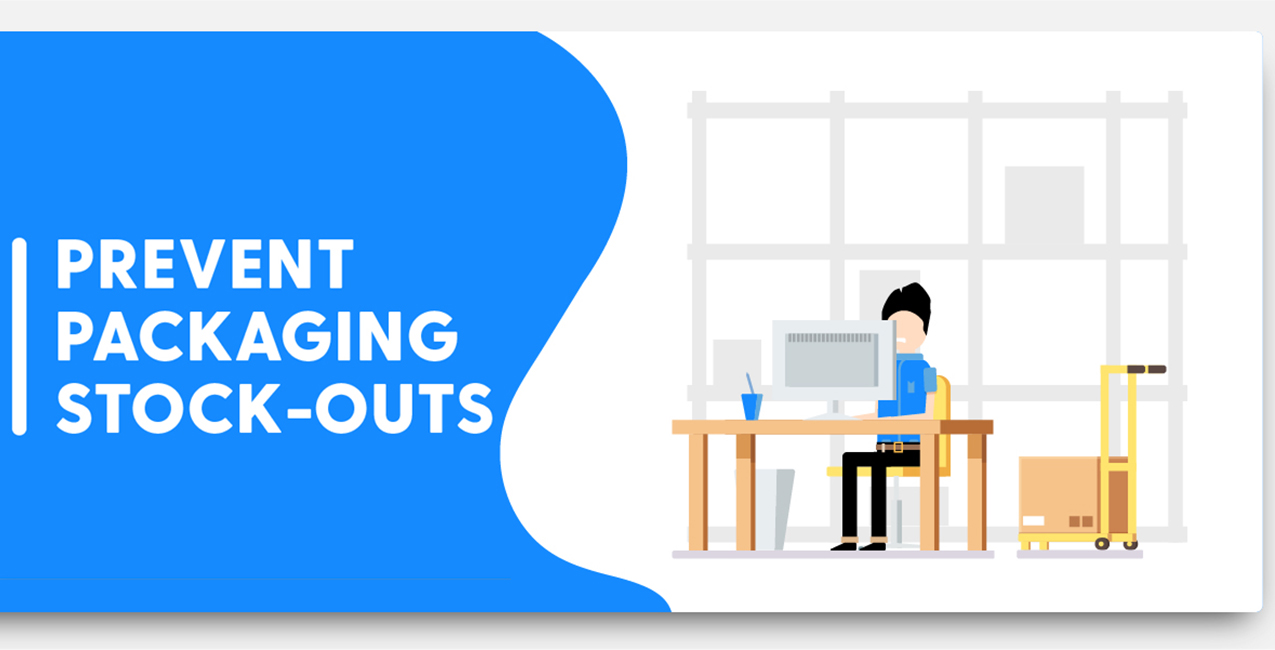
How many zeros in $1 trillion?
In a recent report, it emerged that stock-outs could cause retailers to incur losses worth $1 trillion.
Retailers today have to be quick on their feet to satisfactorily deliver to customers. For the past decade, packaging has come to the forefront. From ‘unboxing videos’ of product packaging to Amazon’s brown box, packaging has become unique and recognizable.
Without the required packaging, products don’t reach their final destination. If the required packaging is not stocked in the warehouse or delivery centers, then it delays deliveries.
In this article, we’ll discuss how packaging stock replenishment can help you in the long run.
Why Packaging Material Stock-outs Happen
Brands today work in dynamic environments. They are finding newer ways to source packaging material. As stock replenishment methods evolve, eliminating stock-outs might be possible. First, let’s explore 3 causes of stock-outs of packaging material inventory.
1) Shifting Market Demand
Very often, brands might underestimate or overestimate product demands. However, in such cases, packaging material stock replenishment can be as unpredictable as a game of odds.
Today, brands are connecting with their customers through social media. They form a community, share early access to offers and give out discount codes to customers on various social channels.
Like the proverbial coin toss, odds are a social media campaign is successful. As a result, the demand for the product rises. Meanwhile, brands scramble to stock the required packaging material. Although brands expectedly build their inventory, they cannot necessarily predict the demand. In short, the possibility of packaging stock-outs can delay product movement.
Read : How to manage packaging inventory for fluctuating trends?
2) Slow-moving Processes
A ready supply of packaging material is fast becoming the backbone of a smooth-sailing supply chain. To that end, inventory management processes are ever-evolving. However, if one process moves at a slower speed, it causes a domino effect and starts a series of delays.
Delays are caused due to various reasons. For instance, misallocation of packaging material or vendors transporting to different locations. Moreover, the quality of the packaging material might be subpar causing time-consuming replacements.
In the same vein, slow-moving processes can cause mismanagement with warehouses, vendors and more. Also, dependency on manual processes might lead brands to work in the dark.
These might snowball into a stock-out scenario. In other words, the cost of stock replenishment can go higher, causing brands to incur huge losses.
Read: 3 reasons you need to automate your packaging vendor management.
3) Lack of Visibility
While managing inventory on a large scale, it’s very easy for human errors to creep in. Often brands don’t habitually refer to any inventory reports or any existing data for stock replenishment.
In inventory management, packaging material can be misplaced, stolen or the SKUs might vary across locations. For instance, a vendor says they have dispatched packaging material, but it might not be the case. Therefore, managers in charge of sourcing or stock replenishment don’t have access to accurate data. Furthermore, they can’t transparently track shipments along the supply chain.
To sum it up...
Packaging stock-outs + No product roll-out = Perfect opportunity for the competition.
At the end of the day, loyal customers look for convenience. With so many options in the market, inefficient packaging material stock replenishment contributes to stock-outs.
Read: How to ensure procure-to-pay visibility?
Let There Be No Packaging Material Stock-outs
So, what can be done to prevent the consequences of stock-outs?
1) Audit Your Inventory
As the financial year rolls around, you will be auditing your processes and finances for a healthier business. Similarly, auditing your packaging material inventory can aid in preventing stock-outs. A recent report says inventory carrying costs will generally total about 20%-30% of the total inventory costs.
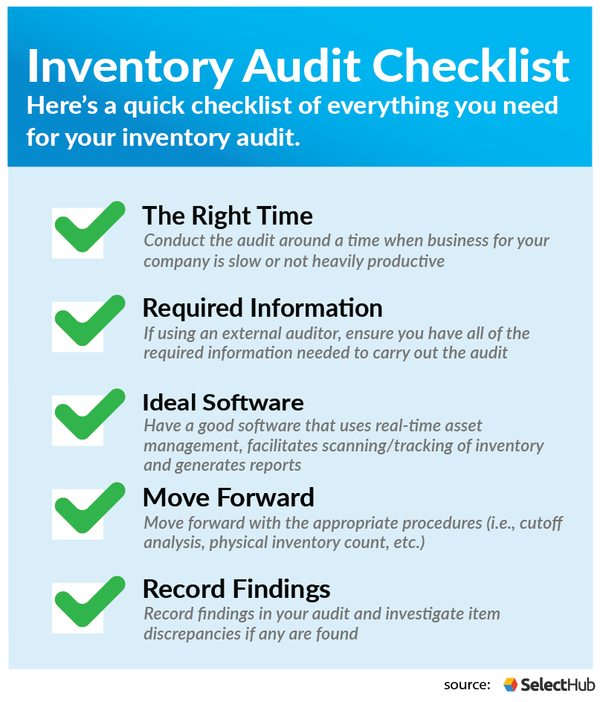
Generate reports according to the above questions for a certain period to keep tabs on what’s working and what's not. Once you know which metrics to track, it can help you make better stock replenishment decisions resulting in total cost optimisation for your packaging.
2) Calculate Safety Stock
There are many reasons a product’s demand can fluctuate. Those include sudden interest in certain products, seasonal fluctuations, reliability of supply chain partners or the success of an advertising or promotional campaign. Therefore, it’s difficult to accurately forecast demands and market trends.
Safety stock cushions the rise and fall of demands.
Calculating your safety stock or buffer stock can help create a no stock-out scenario. If you are running a festive campaign with offers, then safety stock can come to the rescue. It gives you a buffer time to replenish packaging material stock, meet rising demands and eliminate stock-out cost.
How To Calculate Safety Stock?
Safety Stock = Daily Consumption x Lead Time x Safety Factor (for demand fluctuation)
Watch how an automated supply chain platform can ensure 100% availability of packaging for businesses with lower inventory.
3) Determine Your Warehouse Logistics Requirements
Packaging material vendors play an important part in managing an equipped inventory. When they supply the packaging material, that’s when you can meet demands. When they don’t function in a timely and organised manner, there is a high possibility of stock-outs.
Take a pause and analyse the effectiveness of your packaging material supply management.
Research and discover local packaging material vendors. Routinely test the packaging material across locations to gauge quality, quantity, and price. Subsequently, with a hands-on approach, you’ll be able to cut down on the stock-out cost.
4) Automate Reordering System
After establishing your safety stock number, it’s easy to determine the reordering point. Although inventory stock replenishment is a given, often the process is manual. Manually restocking across locations can be resource-intensive and time-consuming.
In a recent retailer survey, 43% stated "overbuying inventory" and 36% chose “underbuying inventory” as challenges within their company. You can improve your stock replenishment process by automating the reordering system. Therefore, based on the rate of consumption, packaging material can be stocked with ease.
Take Control of Your Packaging Material Stock
During the holiday season, USPS expects its holiday parcel volume to hit 800M. FedEx projected they would move more than 33M packages just on Cyber Monday.
Therefore, with brands anticipating such monumental demands, stock replenishment is of the highest priority.
When you automate your packaging material supply, you can deliver products in a timely manner. You’ll be able to offer better customer service and win some loyalty. Plus, you’ll save costs.
Looking to automate your stock replenishment? Get in touch with our packaging material sourcing team today.