Why Is Chemical Packaging a Mindful Task & How to Best Do It?
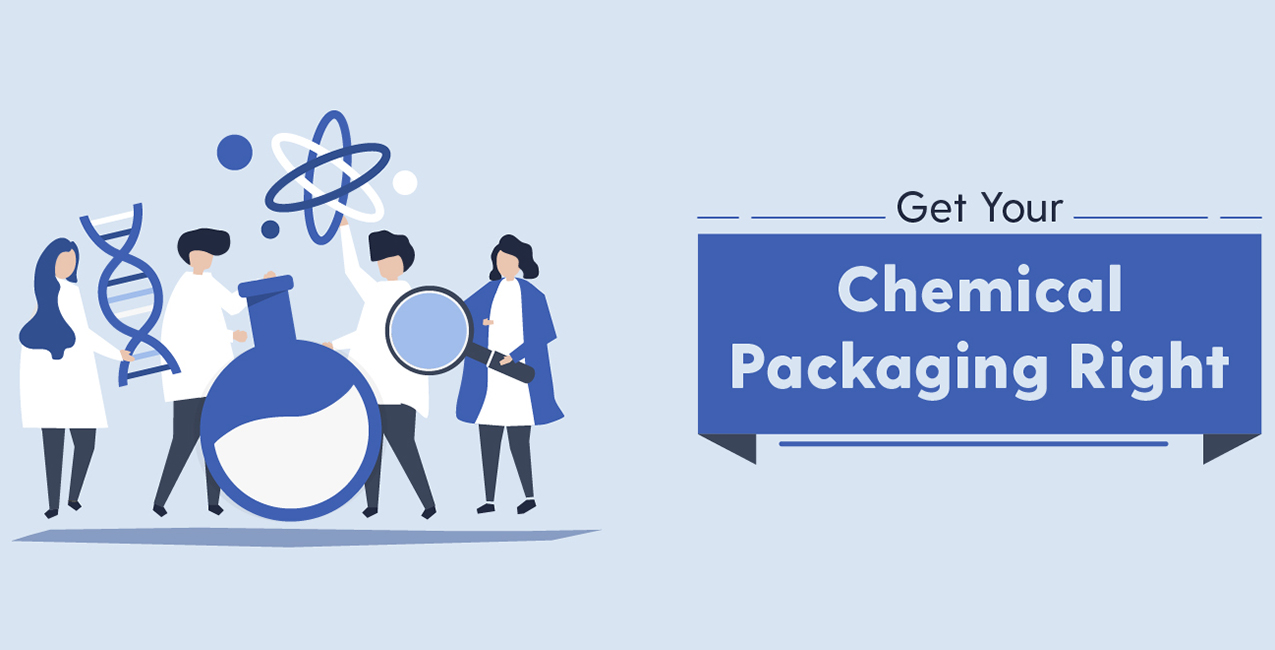
Chemical packaging has always been a challenging task. When packaging a certain chemical compound, the number of options that one have is often quite a few. Plastics have been the primary packaging material. Even though plastics have a negative impact on the environment, in the case of chemical packaging, plastics are the safest. They prevent spillage, they are low cost and also can be reused. However, since usage of plastic is being regulated, alternative chemical packaging solutions are also being explored. If done improperly, the industrial chemical can have a long-lasting negative impact on the environment, can cause harm to the end user or the warehouse workers, or can just be rendered ineffective.
Chemical Packaging Challenges
When it comes to the packaging of industrial packaging, the challenges are manifold. Here are some of the main concerns regarding chemical packaging.
Health Hazards
Industrial chemicals are often critical health hazards. Compounds like acute toxics need to be handled carefully during packaging and shipping. Chemicals that are highly acidic or basic can cause burns when they come in contact with skin. Hence, the packaging process must be automated. Generally, automated fillers are used and the capping is also done automatically with minimal human intervention.
Physical Hazards
Chemicals such as aerosol sprays, alcohols, vehicle fuels, compound rich in hydrocarbons or even pure gases can cause physical harm if not handled carefully. Most of these chemicals are extremely flammable or they support combustion. Aerosol sprays that contain flammable liquids as their bases, such as deodorants, household pesticides and air fresheners commonly come in metallic static-safe cans. Static electricity is an ignition hazard that can ignite the pressurized canisters and cause explosions. That is why vehicle fuel is often transported in vehicles that are electrically grounded. Metal drums are typically used in these cases. The same goes in the case of packaging of pure gases. Sometimes, another non-reactive gas, commonly nitrogen, is mixed with the concentrated gas to reduce the chances of a fire.
Environmental Hazards
Chemical packaging must be able to withstand the elements and prevent the chemical from leaching into the surroundings. For instance, pesticides that often leach away from their packaging cause chronic and acute hazards to the environment, and especially in the water bodies. Solid chemicals that are packed using woven sacks are more prone to causing these hazards. Hence, packaging that will not easily degrade over time, such as glass or plastic containers are often used. Air-tight capping is used to prevent evaporation.
Reaction With Water
A lot of chemicals react with water. Handling them can become quite challenging both for the end users and during the packaging process. The packaging will not only protect the chemical from exposure to moisture but will also allow the end user to use the chemical without causing a hazard. Moreover, they should also work as a decent storage option. Chemicals such as lithium, potassium, and sodium react with water. Such chemicals often come in air-tight plastic jars or metalized multi-layer pouches.
Small, Unique or Numerous Packages
Often chemical products are provided as a two-part product. The packaging will keep the two chemicals separated and protected until it reaches the end user. For instance, two-part epoxy adhesives are an example where two chemicals need to be packed together without mixing them. Bike chain degreaser and lubricant is another example. Often, the bundling can be a challenging task. In such cases, custom chemical packaging can help.
Multiple Products, Colors, Variants
The packaging industry often has to deal with multiple chemicals over a span of a few working days. The slightest presence of the chemical from the previous working day in the fillers can completely ruin the chemicals of the present day. Hence a rigorous clean down is required after each session. Also, to prevent the chemicals from reacting with gases in the air, an inert dry atmosphere is created by purging nitrogen.
Space Limitations
Filling small containers can often be challenging, especially when handling hazardous substances. Monoblock filters and cappers are often better suited than the conventional turnkey or inline systems.
READ: How to choose the Right Size Box?
Alternatively, if your box is not the correct size, read - How to protect your products using void-fill solutions?
Common Chemical Packaging Solutions
Glass Bottles
Glass bottles have been the staple solution for packaging chemicals for a very long time. It was traditionally used for packaging liquids before plastics. Glass does not corrode, is available in multiple shapes, have excellent barrier properties, provides good thermal insulation and can be tinted to prevent exposure to light. Almost all solid and liquid chemicals can be packed in glass containers. They are also reusable and eco-friendly. However, glass containers need to be handled carefully since they are brittle.
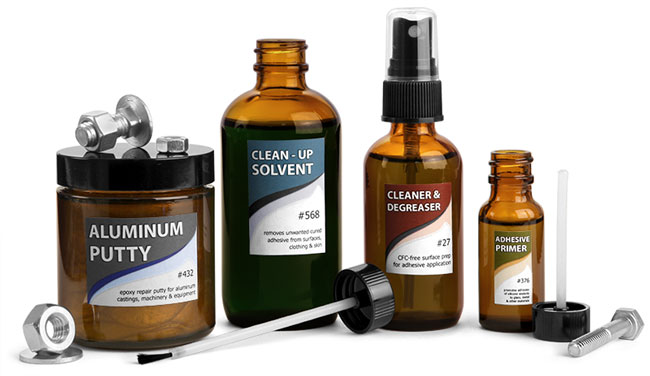
Plastic Jars and Containers
LDPE, HDPE, PVC plastics are now extensively used in packaging chemicals. They are low cost and provides almost all the safety features that a chemical packaging requires. It is easy to add convenience features for end-users when plastic packaging is used. However, due to environmental concerns, plastic packaging is being replaced with other reusable alternatives.
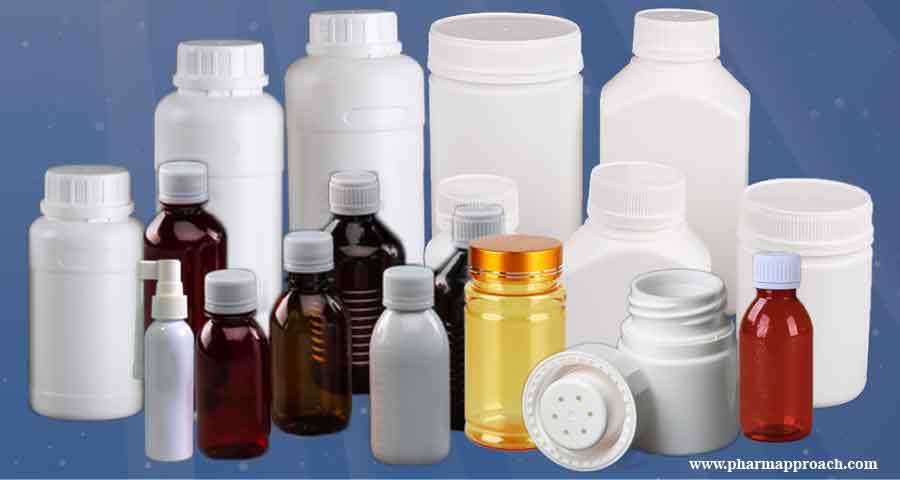
Metal Drums
Metal drums are traditionally used to store flammable liquids, such as petroleum, crude oil, paraffin and so on. The metal container stays electrically grounded and prevents accumulation of static charges that may cause lead to ignition of the chemical. Moreover, metallic drums are cheap, eco-friendly and re-usable.
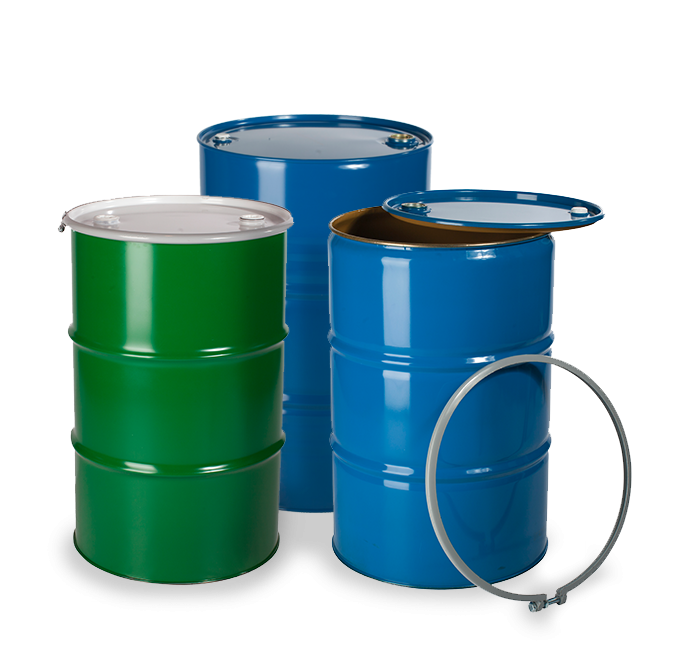
Lacquer Lined Drums
Lacquer lined drums are used especially in cases where the chemical may react with iron or steel. Epoxy lacquer is used to coat the drum to prevent any contact. It is used in packaging for food, pesticides, agrochemicals, and so on.
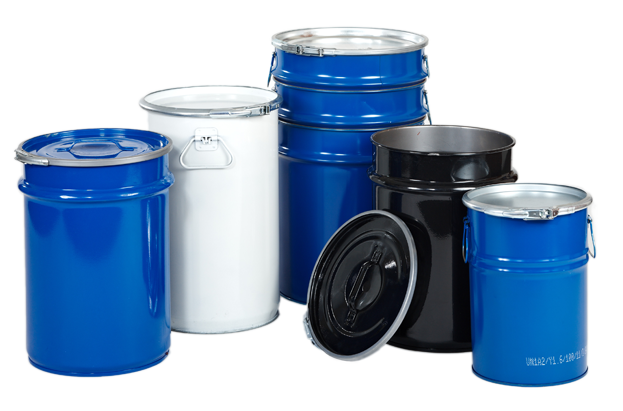
Intermediate Bulk Containers
Intermediate Bulk Containers or IBC is used to pack solid or liquid chemicals in a way that makes them easy to transport. These cuboidal containers are pallet mounted, can be stacked on and are generally made from plastics, with metal supports. IBCs come in many other shapes too, can be flexible or rigid, but all of them have a common feature – that is, the integrated pallet mount. This makes these containers easy to handle different chemical packaging sizes using a forklift.
.jpeg)
You might also like to read about testing methods for packaging.
READ: How to protect fragile products?