Choose the Right Blister Packaging for Your Business
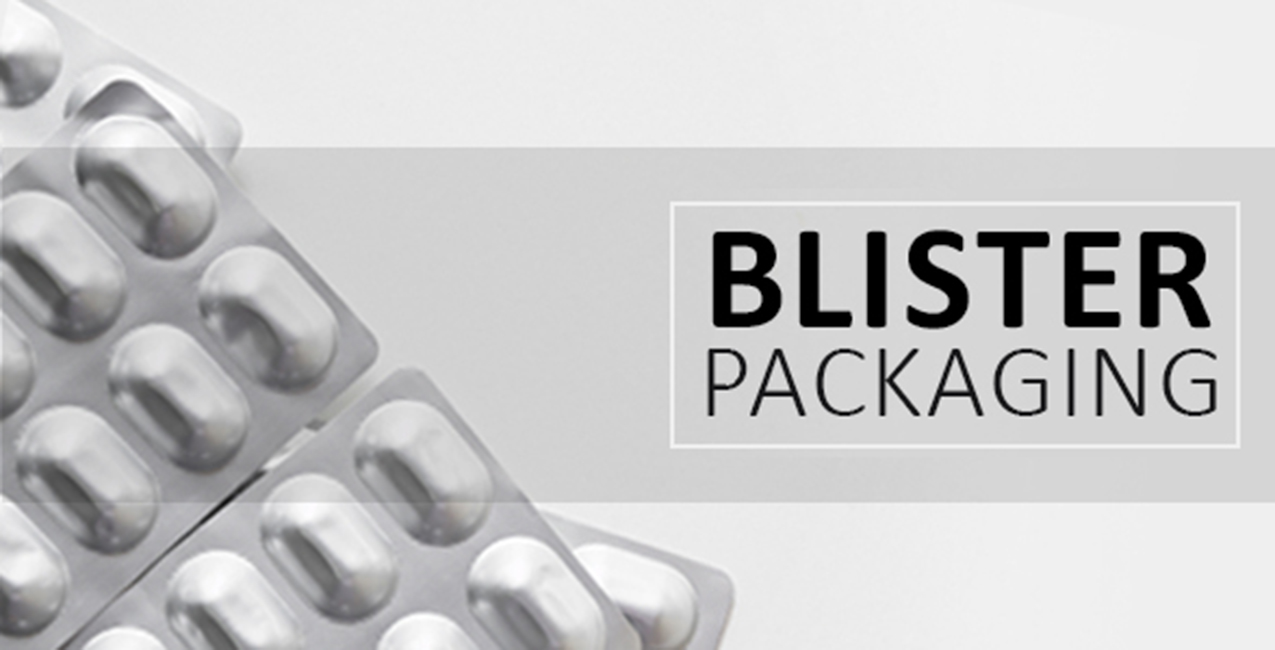
Blister packaging is a form of plastic packaging that is used for small consumer goods and pharmaceuticals. It is mostly made from thermoformed plastics. Blister packs have a backing of paperboard, aluminium foil, or even other plastic sheets.
Where is Blister Packaging Used
Blister packaging, commonly known as unit dose packaging, is used in the pharmaceutical industry for packaging medicine. In blister packaging, a plastic sheet is thermoformed to form multiple cups or blisters that hold the product. Blister packaging is used in multiple areas and not just pharmaceuticals. Blister packs are low-cost packaging that is theft deterrent, tamper evident and provides good protection.
Physical Properties
Blister packaging is made from different types of polymers, such as PVC, PVDC, PCTFE, COP, and a few others. #PVC or polyvinyl chloride is the most common blister packaging material.
The main advantage of using PVC is the low cost. PVC sheets of 0.25 to 0.3mm are used for making blister packs. #PVDC or polyvinylidene chloride is used along with PVC sheets to improve the barrier properties of the packaging. This provides excellent protection from oxygen and moisture.
#PCTFE Polychlorotrifluoroethylene is another form of laminate for blister packaging. PCFTE is primarily used as a moisture barrier. Compared to all the polymers, PCFTE comes with the minimum value of water vapour permeation.
#COP or Cyclic olefin polymers as well as Cyclic olefin copolymers improves the thermoforming in blister packs and even provides good barrier properties. COP, when used with other polymers such as polypropylene and polyethene, allows manufacturers to make blister packs with deep pockets. These are essential for packing medicines.
Blister packaging manufacturers also use cold form packaging made from PVC, aluminium, and Polyamide. The notable physical properties of blister packs are as follows:
- Water resistance: The thermoformed polymer protects the inner contents from water, water vapour or any other liquids. However, the degree of water resistance of the entire packaging also depends on the rear cover. If the blister packaging uses a paper-based sheet for the rear lid, then the water resistance is degraded.
- Barrier properties: Blister packaging provides an excellent barrier from oxygen and moisture. The barrier properties improve as the manufacturing process incorporates more layers of polymers to make the blister packaging.
- UV protection: The transparency of the blister packaging can be controlled and hence how much UV radiation gets in the packaging can also be controlled. Metallized PVC completely blocks all UV radiation and increases the shelf life of perishables.
- Protection from drops, bumps and scratches: Blister packaging can hold a product in place and protect it from drops or accidental bumps. The hard-outer polymer layer also protects the product from any form of scratches.
- Tamper Evident: Blister packs are very hard to reuse. Once a blister pack is opened, it cannot be closed easily at all. Moreover, depending on the implementation, blister packs can also be quite hard to open and requires cutting tools.
- High Product Visibility: Blister packs allow the product to be visible. This allows the consumer to make well-informed choices while buying products. When it comes to medicines, blister packs allow users to have a look at the capsule or tablet directly. This makes it much easier to identify medicines.
Types of blister packs
Blister packs come in multiple types. These are:
Thermoformable Blister Packs
Thermoformed blister packs are the most common. The thermoformable blister packaging process involves heating a sheet of plastic or polymer to a temperature where it can be formed using a mold. Thermoformed blister trays are used in medicine and food packaging.

Face Seal Blister
In this form of packaging, a formed plastic sheet having the shape of the product is heat sealed to a paperboard. A full-face seal blister has the plastic packaging from edge to edge of the packaging.
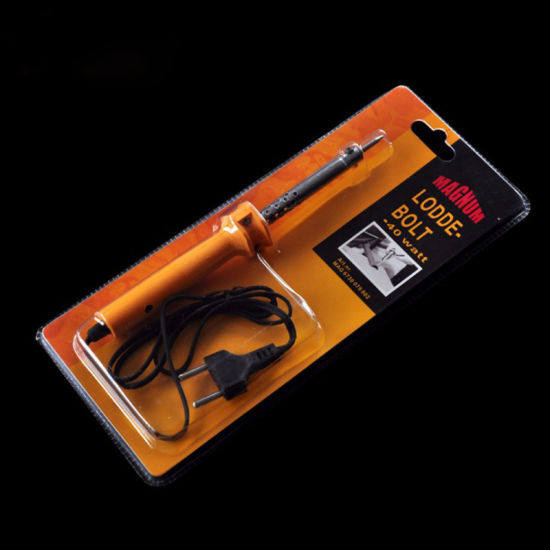
Trapped Blister
This type of packaging uses a single thermoformed sheet trapped inside die-cut cardboard. No sealing tools are required for this.
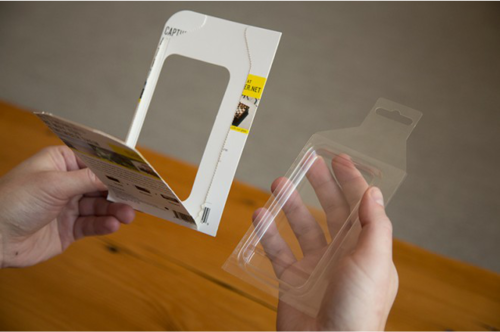
Full Card Blister
Here, the blister extends on all sides and wraps around the paper lid.
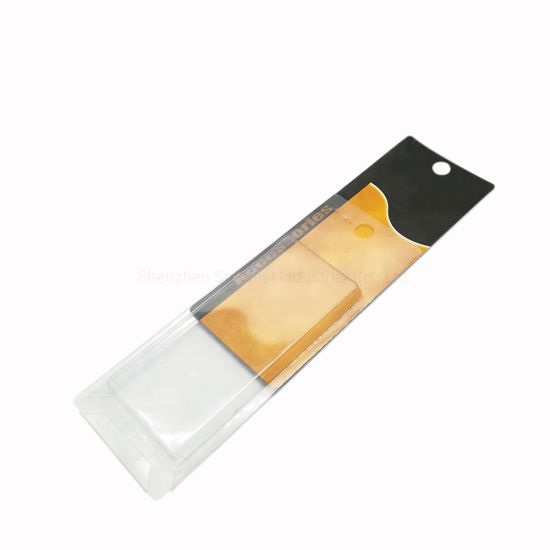
Clamshell
Clamshell is a form of packaging that uses a hinged thermoformed sheet of plastic. This is generally used to pack heavier goods. This type of blister packaging can be reused. A two-piece clamshell is also available that uses two plastic sheets instead of a hinge. A tri-fold clamshell has a bottom stand that allows products to stand upright on store shelves.
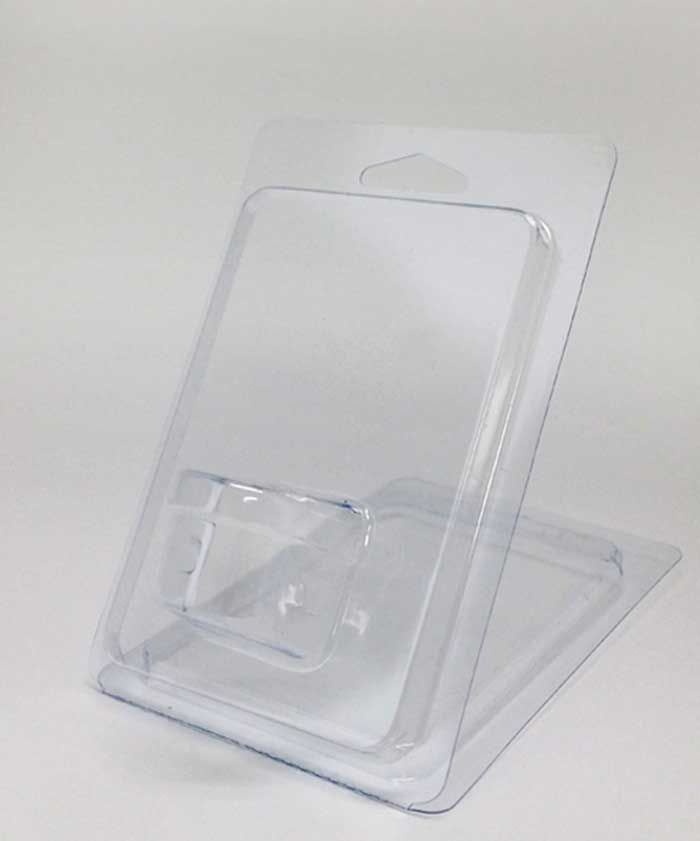
Skin Packaging
This manufacturing technique uses heating and vacuum to form the blisters. The products themselves are used as the molds. The product is sandwiched between heated plastic sheets and the air in the middle part is vacuumed.
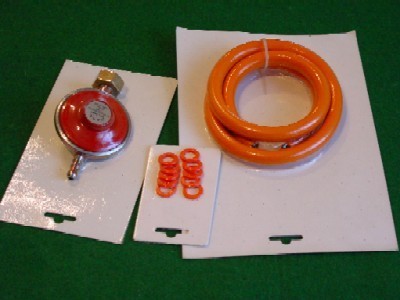
Uses of Blister Packaging
Blister packaging is used extensively in multiple industries. Pharmaceuticals and food industry use it mostly. But it is also used for packing electronics, home improvement tools, stationery and more.
Pros and Cons of Blister Packaging
In spite of having numerous advantages as a low-cost packaging solution as mentioned before, poorly implemented blister packaging has often caused wrap rage. Blister packaging requires a proper sealing tool for heat sealing the package. Metalized plastic sheets used for certain this type of packaging are hard to recycle. Moreover, how effective the protection of a blister packaging will depend a lot on the backing that is used.